Plastic extrusion specialists delivering accuracy and quality
Plastic extrusion specialists delivering accuracy and quality
Blog Article
A Comprehensive Guide to the Refine and Advantages of Plastic Extrusion
In the huge world of manufacturing, plastic extrusion emerges as a crucial and extremely effective procedure. Transmuting raw plastic into constant accounts, it provides to a wide variety of markets with its impressive flexibility.
Recognizing the Essentials of Plastic Extrusion
While it may show up complicated in the beginning glimpse, the process of plastic extrusion is basically simple - plastic extrusion. It is a high-volume manufacturing method in which raw plastic is melted and shaped right into a continual profile. The process begins with the feeding of plastic material, in the form of powders, pellets, or granules, right into a heated barrel. The plastic is then melted making use of a combination of warm and shear, used by a turning screw. When the molten plastic gets to completion of the barrel, it is forced via a tiny opening referred to as a die, forming it right into a wanted type. The shaped plastic is then cooled, strengthened, and reduced right into preferred lengths, completing the process.
The Technical Refine of Plastic Extrusion Explained
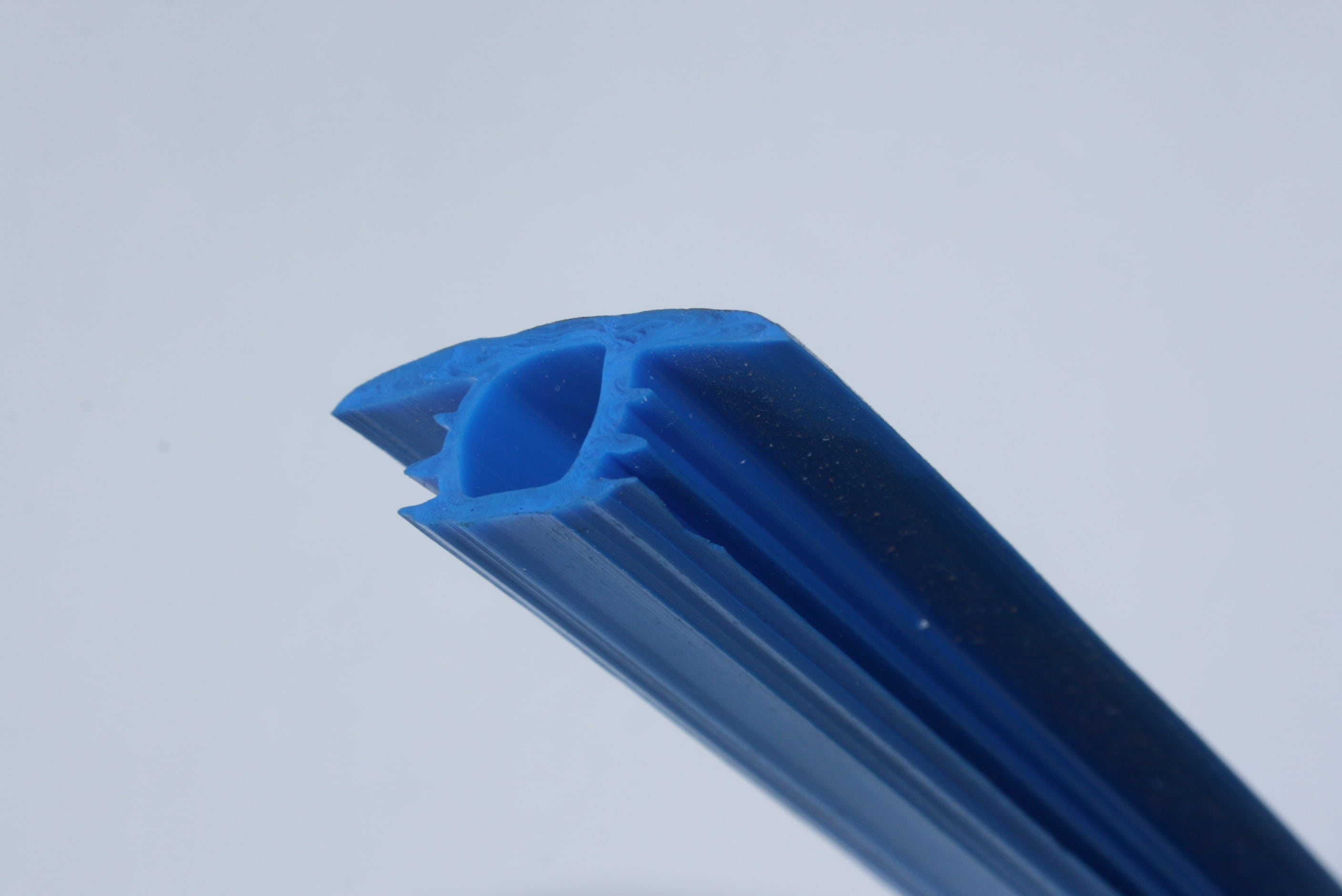
Kinds Of Plastic Suitable for Extrusion
The option of the ideal kind of plastic is an essential aspect of the extrusion process. Different plastics use distinct buildings, making them a lot more suited to particular applications. Comprehending these plastic types can dramatically improve the extrusion process.
Contrasting Plastic Extrusion to Other Plastic Forming Approaches
Comprehending the kinds of plastic appropriate for extrusion leads the method for a broader conversation on how plastic extrusion compares to various other plastic forming approaches. These consist of injection molding, strike molding, and thermoforming. Each method has its one-of-a-kind usages and advantages. Shot molding, for circumstances, is superb for producing complex parts, while impact molding is best for hollow objects like containers. Thermoforming excels at forming huge or shallow parts. Nevertheless, plastic extrusion is unequaled when it comes to producing continual profiles, such as pipelines, seals, and gaskets. It also enables a regular cross-section along the length of the product. Therefore, the selection of approach largely depends on the end-product demands and specs.
Secret Benefits of Plastic Extrusion in Manufacturing
In the realm of manufacturing, plastic i thought about this extrusion supplies numerous substantial benefits. One noteworthy advantage is the cost-effectiveness of the process, which makes it a financially enticing manufacturing method. Furthermore, this method provides remarkable item adaptability and enhanced production speed, thus increasing overall production efficiency.
Cost-Effective Manufacturing Technique
Plastic extrusion leaps to the center as a cost-effective manufacturing method in production. This process sticks out for its ability to generate high volumes of product quickly and successfully, offering suppliers with considerable financial savings. The main price advantage is the capability to use much less pricey resources. Extrusion utilizes polycarbonate products, which are less expensive contrasted to porcelains or metals. Additionally, the extrusion procedure itself is relatively basic, reducing labor expenses. Furthermore, plastic extrusion calls for less energy than typical manufacturing techniques, adding to reduced functional costs. The procedure also reduces waste, as any kind of excess or malfunctioning materials can be reused and recycled, providing another layer of cost-effectiveness. Generally, the economic advantages make plastic extrusion a very attractive option in the manufacturing industry.
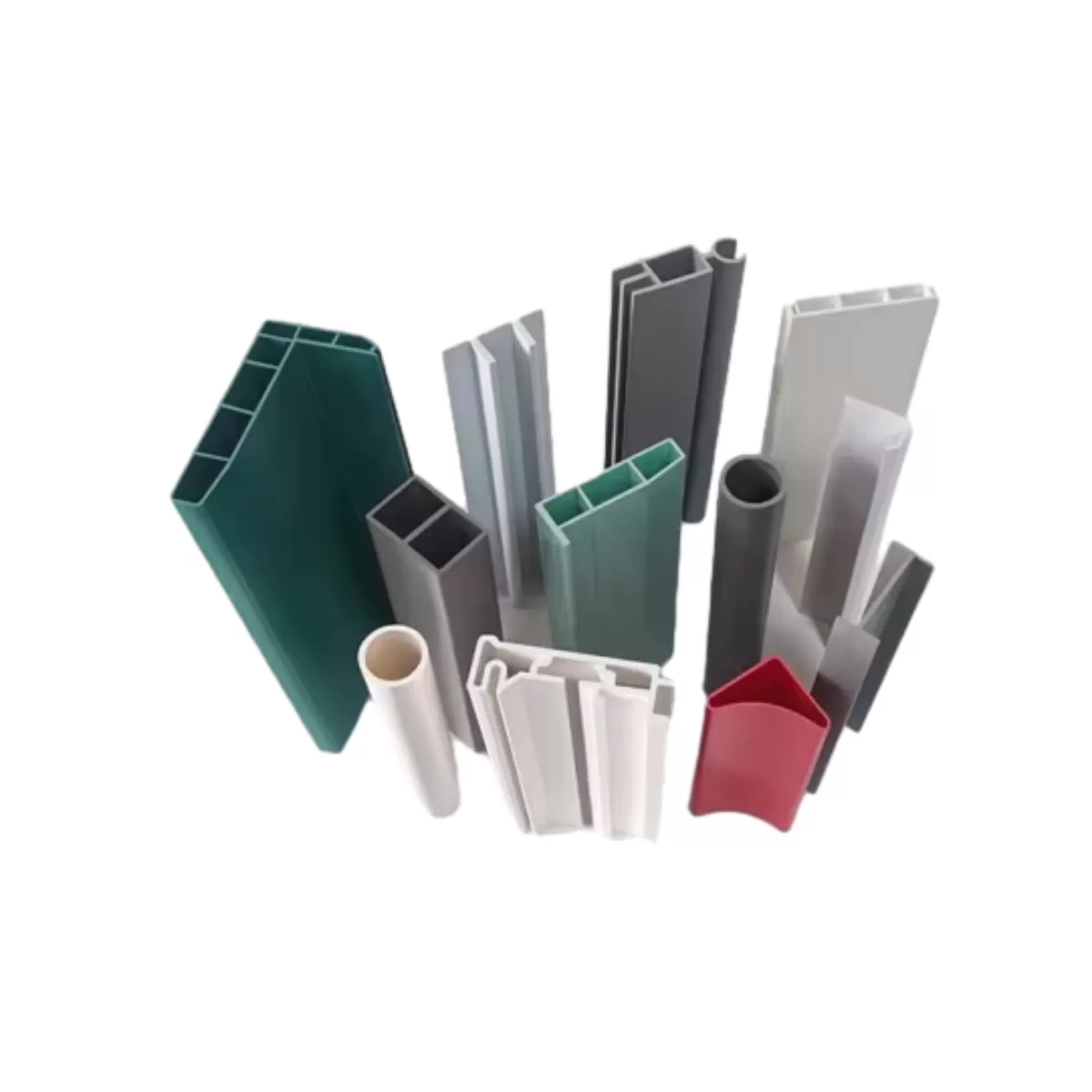
Superior Product Flexibility
Beyond the cost-effectiveness of plastic extrusion, another substantial benefit in making hinge on its remarkable product versatility. This process permits the development of a vast selection of products with varying forms, sizes, and designs, from straightforward plastic sheets to detailed accounts. The flexibility is attributed to the extrusion pass away, which can be personalized to yield the preferred product layout. This makes plastic extrusion an ideal remedy for sectors that require tailored plastic elements, such as automotive, see this website construction, and product packaging. The capability to produce varied products is not only useful in meeting particular market demands but additionally in making it possible for makers to explore brand-new item lines with very little capital financial investment. Essentially, plastic extrusion's product adaptability promotes technology while improving functional efficiency.
Enhanced Production Rate
A significant benefit of plastic extrusion lies in its enhanced manufacturing speed. Few various other manufacturing processes can match the speed of plastic extrusion. In addition, additional hints the capacity to preserve consistent high-speed production without giving up product high quality sets plastic extrusion apart from various other techniques.
Real-world Applications and Effects of Plastic Extrusion
In the realm of production, the method of plastic extrusion holds profound significance. This procedure is commonly used in the manufacturing of a range of items, such as plastic tubing, window structures, and weather condition stripping. Because of this, it significantly influences fields like building, product packaging, and vehicle industries. Its effect expands to daily things, from plastic bags to toothbrushes and non reusable cutlery. The financial benefit of plastic extrusion, mostly its high-volume and cost-effective result, has changed manufacturing. The environmental influence of plastic waste stays a problem. Therefore, the market is persistently pursuing advancements in biodegradable and recyclable materials, suggesting a future where the benefits of plastic extrusion can be maintained without endangering environmental sustainability.
Final thought
To conclude, plastic extrusion is a highly efficient and efficient approach of changing raw materials into diverse products. It supplies numerous benefits over other plastic creating approaches, consisting of cost-effectiveness, high outcome, very little waste, and design flexibility. Its influence is exceptionally felt in various markets such as building and construction, auto, and customer items, making it an essential process in today's manufacturing landscape.
Diving much deeper into the technological procedure of plastic extrusion, it begins with the selection of the ideal plastic product. Once cooled down, the plastic is cut into the required sizes or wound onto reels if the product is a plastic movie or sheet - plastic extrusion. Contrasting Plastic Extrusion to Other Plastic Forming Approaches
Understanding the kinds of plastic appropriate for extrusion leads the method for a broader conversation on exactly how plastic extrusion piles up against various other plastic developing approaches. Few various other manufacturing procedures can match the speed of plastic extrusion.
Report this page